How many units did you sell? You know that sales were $10 million in the quarter. Those mugs-with-swear-words-on-them had an average cost of 5 bucks each; you sold them for an average wholesale price of 10 bucks a pop. So you sold 100,000 units.
That's it. Unit sales: 100,000. Easy.
Related or Semi-related Video
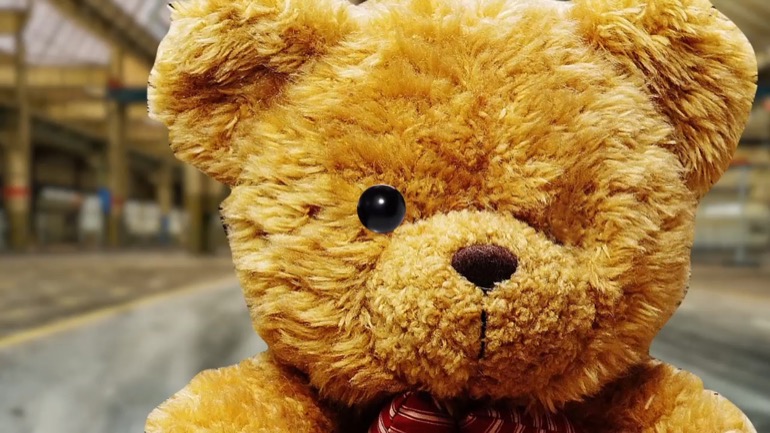
Cost Accounting: What is Process Costing...0 Views
and finance Allah shmoop What is processed Costing shmoop old
All right People like the name says process costing helps
you figure out well the cost of the process But
which process All right well here we're talking about manufacturing
process costing helps companies determine how much it'll cost them
to make each individual product they manufacture Firms use the
technique to assign the expenses related to manufacturing to each
of the units they produce The process works best in
cases of mass production Yeah lots and lots of identical
items getting made in mass production If you're carving custom
totem poles by hand while process costing won't really come
into play or help you much however much it costs
you to make that one totem pole Well that's just
what it cost you But when you're cranking out giant
patches of the same product while process costing tells you
how much money to assign to the manufacture of each
little unit Okay so you run a company that makes
the eyes that go into teddy bears You don't make
the teddy bears themselves You're actually scared of stuffed animals
Long story involving a haunted teddy He tried to kill
you as a kid although while the memory is a
little foggy but you can emotionally handle making just the
eyeballs So your company makes millions and millions of little
black buttons that you ship off to teddy bear factories
all over the world All your eyes are the same
You make 1,000,000 eyes a month The only material you
need is the plastic will Buying the plastic to make
1,000,000 eyes cost you 100 grand Meanwhile the cost of
paying your workers plus the expenses associated with running cutting
shaping and stamping machines well all that together comes to
150 grand Using advanced calculus you determine that the material
cost for the 1,000,000 eyes or 10 cents and I
the labor and machine expenses known as your conversion costs
are 15 cents and I The total cost for the
process is 25 cents and I a total of 250
grand for materials in conversion cost divided by the 1,000,000
eyes you just produced Well the simple division works because
each eye's essentially identical You can assume that each one
took an equal amount of time an equal amount of
plastic an equal amount of machine power to produce and
labor to produce the adult get labour in a single
product factory process costing doesn't provide much insight but when
there are multiple products the strategy is essential to understanding
profit margins for the various products Will you start a
second business line to sell eyes for dolls You also
have a fear of dolls because of that time your
sister locked you in her closet over night A lot
of years of therapy spent on that one Thanks Susie
Well the doll eyes and the teddy eyes used the
same plastic and the same machines and the same labour
Under the new setup you're making 750,000 eyes 500,000 doll
eyes The plastic costs you 200 grand a month The
cost of the machines and labor total 150 grand so
in total you're spending $350,000 to manufacture 1.2 5,000,000 eyes
Do the math each I cost 28 cents per I
know that right Not quite The doll eyes required twice
the plastic as the teddy eyes However they only need
2/3 of the time in the machines and only 2/3
of the labor time to create So here's where process
costing earns its keep The goal here is to take
these general costs and apply them to the specific products
Right So you're spending 200 grand a month on plastic
to make 750,000 teddy eyes and 500,000 doll eyes That's
1.2 5,000,000 eyes total including those for both dolls and
Eddie's But the doll eyes take twice as much plastic
to make throw everything into the process costing mathematical blender
and you end up with wealth 10 cents and I
for the teddy version and 20 cents and I for
the doll version So now let's do the same thing
with the other costs While 150 grand total for all
production doll eyes used 2/3 of the resource is as
the teddy eyes math blender Again we get 10 cents
for the doll eyes and 15 cents from teddy eyes
Total cost for the two products 25 cents for the
teddy eyes and 30 cents for the doll eyes So
process costing shows us that doll eyes arm or expensive
to make by a fair amount than the Eddie eyes
Full time for the annual board meeting You have money
for a marketing push and the board wants you to
recommend which product to push harder Eddie eyes or doll
eyes Well the teddy I sell for 35 cents each
and the doll I sell for 51 cents each Well
the process costing we did shows us that the teddy
product cost 25 cents to make And if they sell
for Roel 35 cents that means that there's a 10
cent gross profit on each sale Divide that 10 cent
profit by the 35 cents in revenue each one brings
in and well gross margins on those then come in
about an 29% The doll product cost 30 cents to
make with a 51 cent sales price The gross profit
on each eye is then 21 cents which means gross
margin just over 41% So the doll eyes while more
expensive to make our ah higher margin product because they
sell for so much more you recommend a marketing push
for the doll eyes information you wouldn't have had if
you didn't go through the process costing rigmarole like we
just did here It makes process costing a very useful
tool when you're mass marketing or mass producing multiple products
and yet can't say the same for the totem pole
subsidiary you're thinking about you know getting off the ground
Each totem pole there takes a different amount of time
and different amount of materials and we'll each has different
machine costs associated with its production But at least you
know when you carve out the animal faces you'll have 00:05:12.789 --> [endTime] the eyes all ready to go
Up Next
What is a Cost: Cost Versus Expense? Cost and expense are pretty similar terms when looking at traditional definitions but they’re a little diffe...
How can unit fixed costs mislead the misled? Unit fixed costs can be misleading because the fixed cost per unit decreases as production increases;...